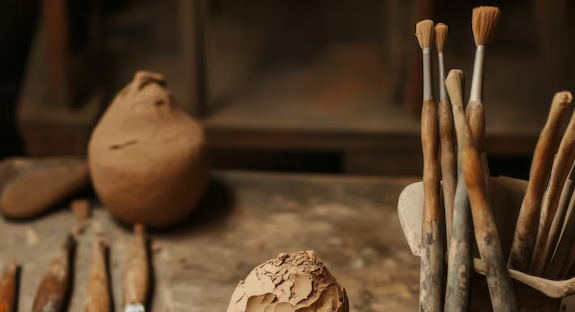
Process & Payment details
What is the process ?
Step by step guide
What is the process ?
Step 1
After you have filled out the contact us form with information on what you would like commissioned, we will guide you through the prices, discuss the size and other details needed to start working with you, our patron. We will require photographs and as many details as possible to help get all the aspects correct to achieve a true likeness in the sculpture we produce.
An initial payment will be required after you have been given a quote in order for us to continue, this covers material and labor costs leading up to the casting process.
Step 2
After receiving the initial payment, depending on the project type, a rendering in 2D or a 3D model will be made for your review. After receiving your approval to begin, we construct a full size frame, called an armature. This structure is then filled with a foam core to provide a base for the clay. The foam core is coated to provide a seal, after this stage we’re ready to begin applying hot clay to the frame. We will send progress pictures and spend many hours molding and sculpting every detail. Most monument sculptures/statues are made in sections depending on how big the final piece is, these sections are put back together in the final stage.
Once you are happy with the clay model that has been created and wish to proceed with the mold and casting the bronze, the final payment will be needed. This is the total balance of the original quote minus the initial payment for materials & labor.
Step 3
The next step in our process is to create a positive wax replica of the original clay sculpture using the molds from the clay. We go over every inch of the wax replica, repairing any imperfections such as air bubbles & seams. This process is referred to as wax chasing.
Step 4
Once a perfect wax replica is made, we proceed to create a ceramic shell by dipping it into a mixture of slurry several times. The slurry dries into a ceramic which forms a hard, durable shell that can withstand the extreme temperatures of molten bronze. This is often referred to as an investment casting. The wax replica is then melted out of the ceramic mold. This is called Lost Wax Casting and is an ancient technique that has been used for thousands of years.
Step 5
Bronze is then heated to temperatures nearing 2250˚F so that liquid bronze can be poured into the ceramic molds. Once liquid bronze is poured into the ceramic shell, it is left to cool for several hours before being removed from the molds.
Step 6
Once cooled the ceramic casts are broken open, with large monuments the final raw pieces are welded together. Sandblasting is required to remove remnants of the ceramic mold. Any welds are resurfaced or sanded down perfectly. Finally the desired patina or surface coloring is applied using a variety of chemicals and heat. This is the amazing bronze casting process that requires many skilled artists and craftsman. We’d love to work with you to make a beautiful timeless legacy for many generations to come!
Please click the button below to get in touch if you have any questions.